Expertises métiers
S&OP – Planification des ventes et opérations
Le S&OP est un outil opéré par la supply chain et permet le pilotage tactique de la planification des ventes et des opérations. Notre offre accompagne la mise en œuvre de processus S&OP/IBP structurés et efficaces en intégrant les trois piliers essentiels « People, Process & Tools » pour améliorer la performance globale et la compétitivité de votre entreprise.
Nos convictions
Décider au bon niveau
- Garantir la mise en œuvre de la stratégie d’entreprise par la Direction à l’aide du processus S&OP à travers des décisions clés et des arbitrages entre des scénarios.
- Pilotage des processus S&OP/IPB par les départements Supply Chain et Finance afin d’associer les objectifs aux contraintes
- Décliner les autres décisions par les acteurs du S&OP dans les bonnes unités d’œuvres par départements
Segmenter les pilotages et les décisions
- « One size doesn’t fit all » : Classer vos produits, services et marchés permet d’adapter les processus de pilotage, décisions et actions…
- Adapter le niveau d’analyse et les décisions prises aux enjeux de chaque segment en fonction des contraintes et risques identifiés. Ceci inclut l’adaptation de la stratégie du S&OP aux spécificités de chaque segment.
Enrichir la demande
- Les prévisions statistiques ne suffisent plus et nécessitent un enrichissement collaboratif entre les organisations locales et centrales, ainsi qu’entre le Commerce et la Supply Chain.
- Scénariser la demande afin d’anticiper les variations et d’améliorer la prise de décision en utilisant des techniques de demand planning
- Algorithmes, Machine Learning et IA, en collaboration avec les équipes, facilitent la gestion de la demande (clustering, tendances, promotions, anticipations de déploiement…).
Gérer par les risques et les contraintes
- Identifier clairement les contraintes traitées et pilotées en S&OP/IBP (ressources, cash, approvisionnements critiques…)
- Statuer clairement sur les leviers actionnables par horizon pour adapter à temps vos ressources aux contraintes et besoins
- Définir une stratégie commune de réponse pour accélérer la prise de décision
- Mettre en place un processus de gestion des risques et exceptions à traiter en S&OP
Intégrer l'ensemble des équipes dans les processus
- Faire accepter à l’ensemble des participants et décideurs le besoin de compromis
- Faire comprendre que l’outil ne fait pas tout : Indispensable pour une collaboration mais insuffisant si les acteurs ne partagent pas la même vision
- Accepter d’apprendre de ses erreurs dans une démarche d’amélioration continue et renforcer la résilience de l’organisation
Nos solutions et savoir-faire
Construction des processus de bout-en-bout
- Conception d’un processus robuste S&OP et adapté aux besoins spécifiques avec les équipes (RACI)
- Construction des rituels collaboratifs et multi-horizons permettant de les supporter
- Propositions de schémas d’organisation (multi-niveaux et matriciels) pour adapter la construction du processus
- Assurance de la cohérence des strates de planification du S&OP/IBP jusqu’à la réalité du terrain en passant par le budget
- Rationalisation et déploiement des KPI nécessaires au pilotage
Digitalisation des processus S&OP
- Cartographie de vos SI actuels et rationalisation des choix technologiques
- Sélection de la solution adaptée parmi ERP, APS, CPM, EPM
- Proposition des modules accélérateurs « clé en main » bâtis avec des outils EPM tels que Board et Anaplan (maquettes préconstruites pour faciliter la mise en place)
- AMOA métier sur l’ensemble de la transformation (pilotage, écriture des cahiers de charges, recettes, etc.)
- Alignement des Master Data pour garantir la pertinence de l’ensemble
- Intégration des innovations technologiques (Machine Learning, IA) pour une valeur ajoutée maximale
Conduite du changement
Conception et accompagnement à la mise en place des premières expérimentations opérationnelles (POC)
Accompagnement de la transformation en coachant tous les acteurs via des ateliers et formations autour du S&OP
Alignement de tous les acteurs et directions vers un objectif commun via des indicateurs
Définition et mise en œuvre d’une feuille de route pour accompagner le changement, du CODIR aux opérationnels du S&OP
ZOOM SUR NOS FORMATIONS
Nos certifications et formations
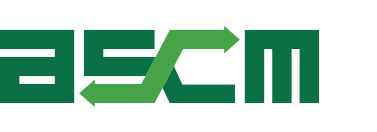
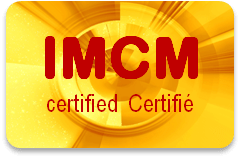
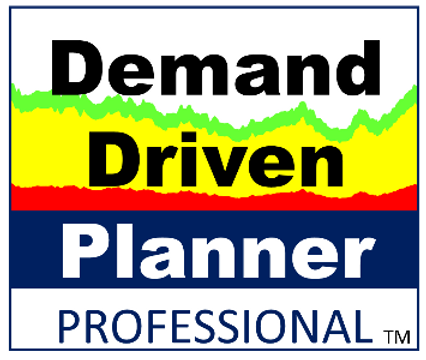
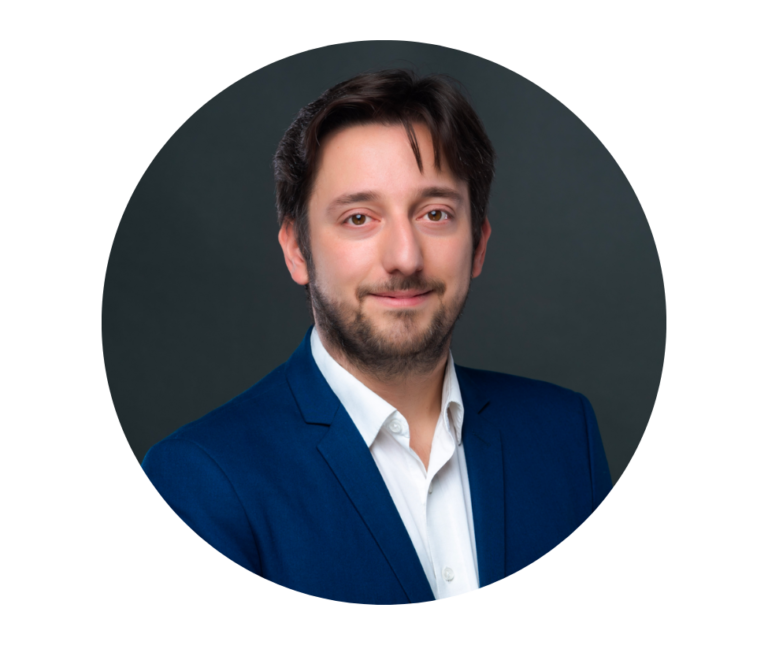
Un projet ? Contactez-nous
Associé, responsable Conseil supply chain
Directeur au sein de Citwell et responsable du bureau Lillois, Raphael a débuté sa carrière chez Decathlon où il a travaillé pendant 6 ans au sein de leur supply chain (opération et projet)
Riche de son expérience dans la transformation des modèles opérationnels, Raphael accompagne ses clients dans l’amélioration continue et leur développement à long terme.
Au cours de sa carrière, il a dirigé d’importants projets autour de la supply chain : transformation des processus, construction d’une vision stratégique, planification de bout-en-bout, gestion des stocks (composants et produits finis).
Parmi nos références
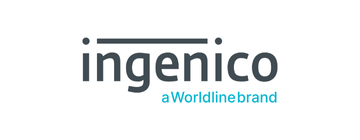
Implémentation d’Anaplan et refonte du S&OP des Terminaux
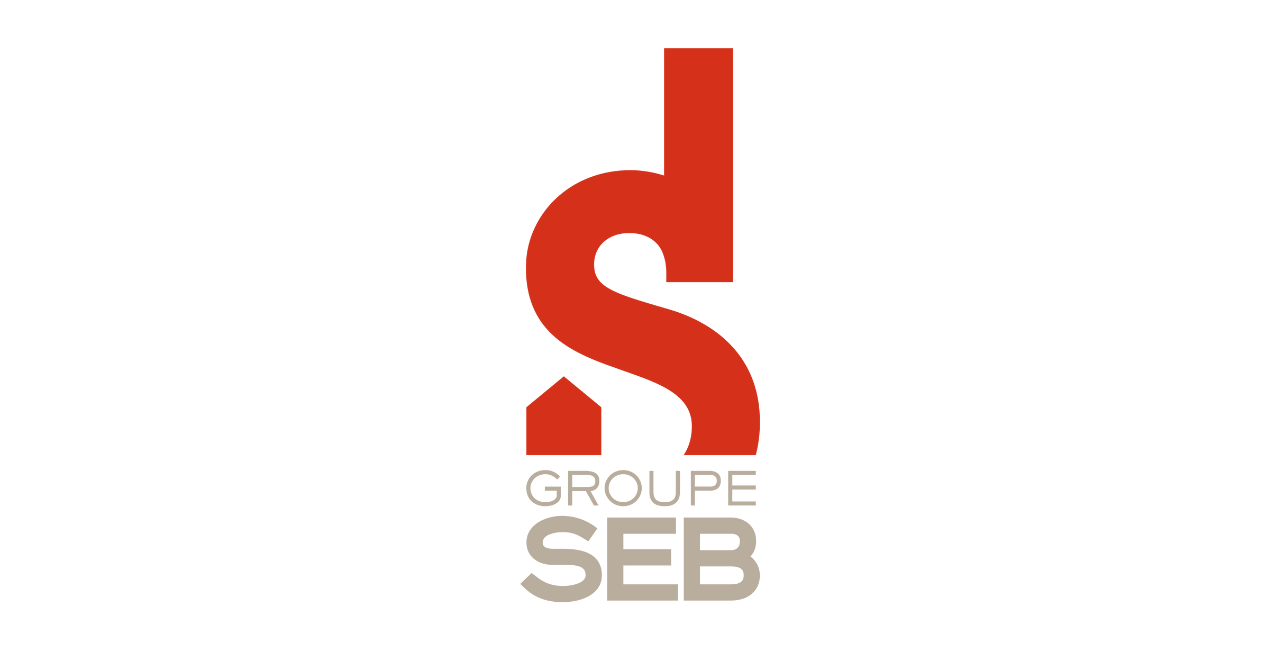
Refonte et digitalisation du processus S&OP sous Board
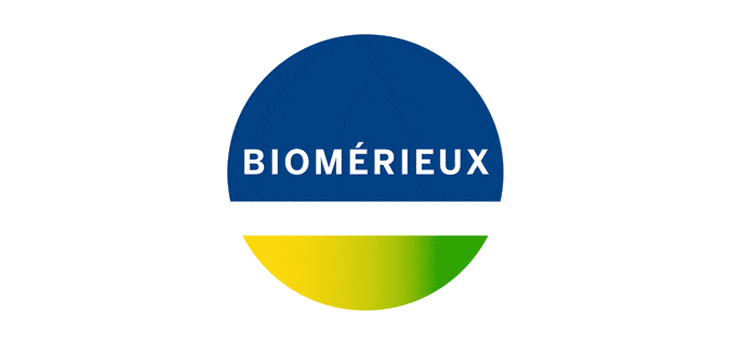
Etude de faisabilité IBP, feuille de route IBP et prévisions
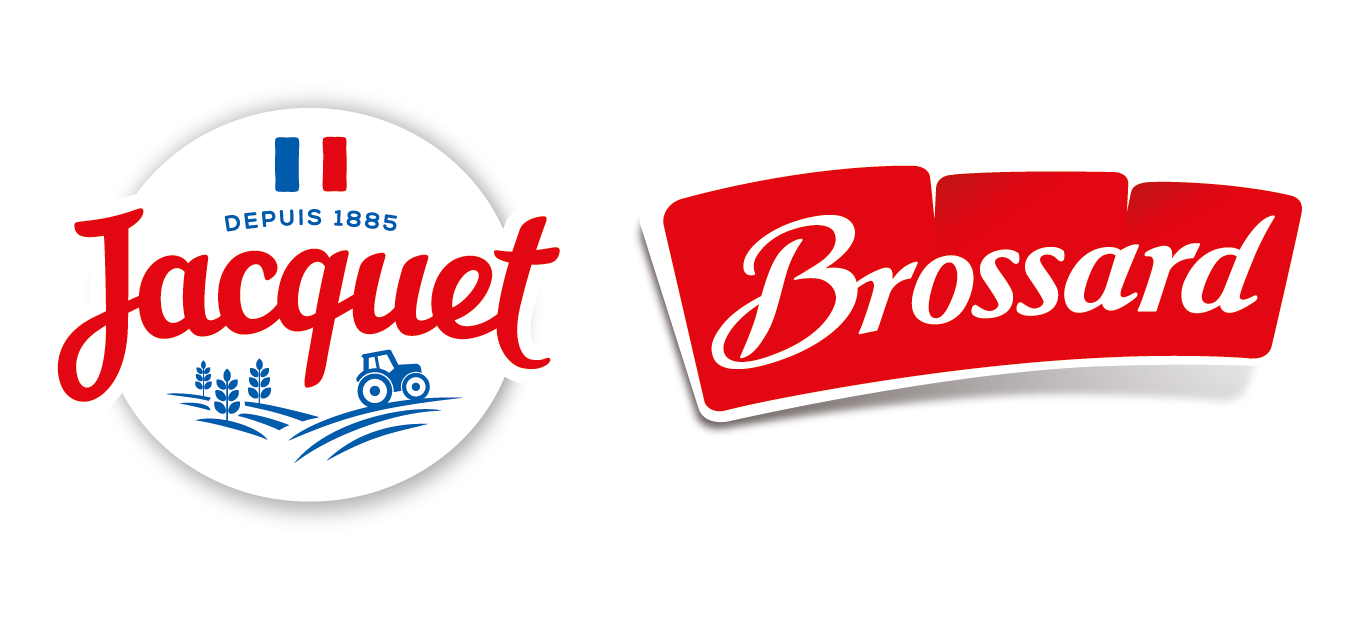
Définition et accompagnement à la mise en œuvre de processus Prévision et S&OP
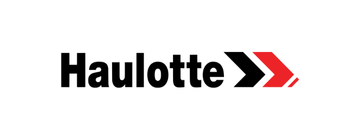
Support à la mise en œuvre des processus et outils de gestion de la demande (DynaSys)
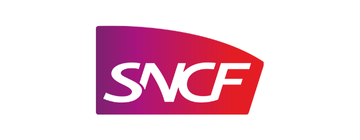
Etude de faisabilité : Hybridation entre un APS et le DDMRP autour d’une boucle clef : DD S&OP
Ils témoignent
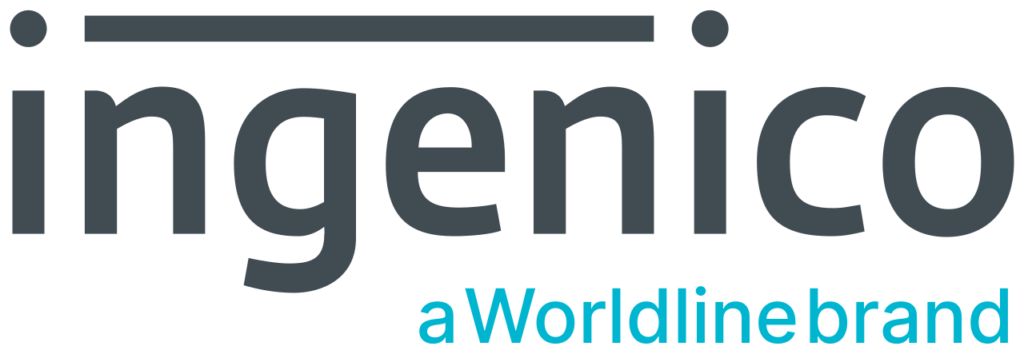
« Citwell nous a accompagnés sur la mise en place d’un S&OP digitalisé. Après une phase de diagnostic, nous avons déployé un plan d’actions adapté aux différents acteurs, en fonction de leur niveau d’adhésion sur le projet. Ce processus S&OP a permis de rendre un meilleur service aux clients tout en optimisant le niveau de stock. »
Kenza Maalouf Supply Chain Project Manager d’Ingenico
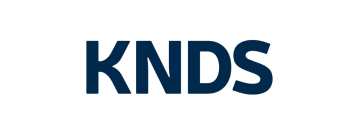
« Citwell est un allié clé dans la conduite au changement et la réorganisation de notre supply chain, pour répondre d’une part aux besoins en compétences en interne et également pour faire face aux enjeux de croissance de notre secteur d’activité. »
Olivier Himpe, Directeur Supply Chain, Business Unit Services Clients de Nexter (KNDS)
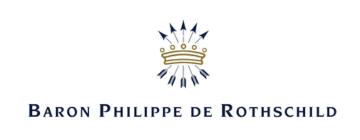
« L’éclairage de Citwell a incité nos partenaires à mieux gérer leurs stocks de bouteilles, pour faire baisser les coûts de l’ensemble de l’organisation. Nous recommandons Citwell pour son pragmatisme, son sérieux, son agilité. »
Frédéric Mairesse, Directeur Général de Champagne Barons de Rothschild
Nos dernières actualités S&OP
Évènement
Replay WEBINAIRE Board et Citwell | S&OP | C’est compliqué de faire simple !
Un cycle S&OP réussi, c’est le juste niveau de données, pour pouvoir prendre de façon agile et rapide, des décisions structurantes pour l’activité sur un […]
- Article
Évènement
Interview de Nicolas Henry pour Supply Chain Magazine : Comment évoluera la supply chain à horizon 5 ans ?
Découvrez notre expertise durabilité et RSE Dans un entretien exclusif avec Supply Chain Magazine, Nicolas Henry, Directeur Associé chez Citwell, partage sa vision sur l’évolution […]
Évènement
Replay table ronde : Mettre en place le S&OP avec quelle organisation et quels outils ?
Replay table ronde : « Mettre en place le S&OP avec quelle organisation et quels outils ? » organisé par Supply Chain Village – Le […]
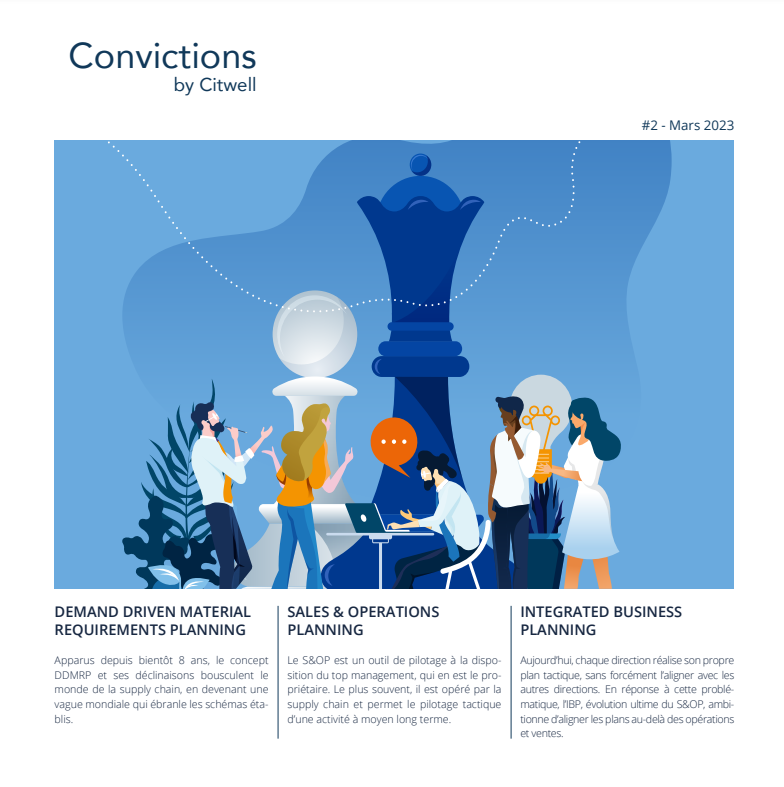
- Publication
Évènement
Convictions #2, le magazine du groupe Citwell
Découvrez le deuxième numéro du magazine du groupe Citwell sur la thématique de la “Planification”. A l’heure où toute prévision est osée, où tout engagement […]